Compact Footprint
Rigid, compact design to reduce floor space
6 Coordinate Systems
Allows up to 6 jobs to be run consecutively in a single set up
3 Step Control of EDM Parameters
Program up to three EDM parameter settings per hole to improve hole quality on difficult entrance and exits
Automatic Electrode Changer (optional)
Allows for a large volume of unattended operation
Automatic Electrode Stabilizer
Moves automatically to provide extra support for long electrodes
1000 RPM Programmable Spindle
Rotation speed is adjustable and will reduce cycle time for some applications
Windows Based
With conversational G and M Code programming
Multi-Tasking Abilities
Create and edit one program while the machine is running another
Ethernet Connectivity and USB Support
For programming and transferring of data
Automatic Depth Control
Generate blind holes reliably without operator intervention
Linear Glass Scales with 1 Micron Resolution
Provides true, closed loop, position feedback for precise part positioning accuracy
Auxiliary I/O
Ability to interface with ancillary devices such as rotary tables, indexers, and work piece handling systems
Integrated Rotary and Tilt/Rotary Tables (optional)
Programmable tilt and rotary systems for complex parts requiring multi axis positioning
Break Through Detection (optional)
Ensures a complete hole or helps to eliminate back wall strikes
Optical Inspection System (optional)
High resolution video camera can measure hole size, verify position, and locate datum points for part programs
EDM Power Booster (optional)
Increases the maximum average current which will reduce the cycle time when using larger diameter electrodes
EDM Milling (optional)
EDM mill shaped diffuser holes using standard cylindrical electrodes
6 Point Probing (optional)
Probe the work piece to determine its 5 axis location and offset position in the part program
Coaxial Flush (optional)
A special guide and guide sleeve delivers auxiliary flush down the guide body
Programmable High Pressure Flush (optional)
Adjust the high pressure flush pressure through the electrode with a G-Code in the part program
TRAVEL | |
X Axis | 15.7″ (400 mm) |
Y Axis | 11.8″ (300 mm) |
W Axis | 16.9″ (430 mm) |
Z Axis | 15.7″ (400 mm) |
Open Height* | |
Minimum | 1.5″ (40mm) |
Maximum | 18.5″ (470 mm) |
Open Height To Tilt Rotary Table** | |
Minimum | 0.0″ (0mm) |
Maximum | 9.4″ (240 mm) |
WORK TABLE | |
Width x Depth | 22.0″ x 17.3″ (560 x 440 mm) |
WORK TANK | |
Width x Depth x Height | 34.4″ x 29.5″ x 5.9″ (875 x 750 x 150 mm) |
WEIGHT CAPACITY | |
On Work Table | 770 lb. (350 kg.) |
On Tilt Rotary Table** | 77 lb. (35 kg.) |
GENERATOR | |
Maximum Average Current | 30A, 60A** |
On and Off Time | 1 to 99 μs |
Capacitors | 0 to 1.81 μF |
AUTOMATIC ELECTRODE AND GUIDE CHANGER | |
AEC Positions | 20** |
AGC Positions | 12** |
FLOOR SPACE AND WEIGHT | |
Width x Depth x Height | 71″ x 77″ x 100″ (181 cm x 196 cm x 254 cm) |
Machine Tool Weight | 3,630 lb. (1,650 kg.) |
ENVIRONMENTAL | |
Room Temperature | 68 to 77°F (20 to 25°C) |
Relative Humidity | 40%to 55% |
UTILITIES | |
Electrical | 220VAC±10%, 3 PHASE, 60 Hz, 3.5 KVA |
Air | 90 PSI@ 1 CFM (6 BAR@ 1.7 CMH) |
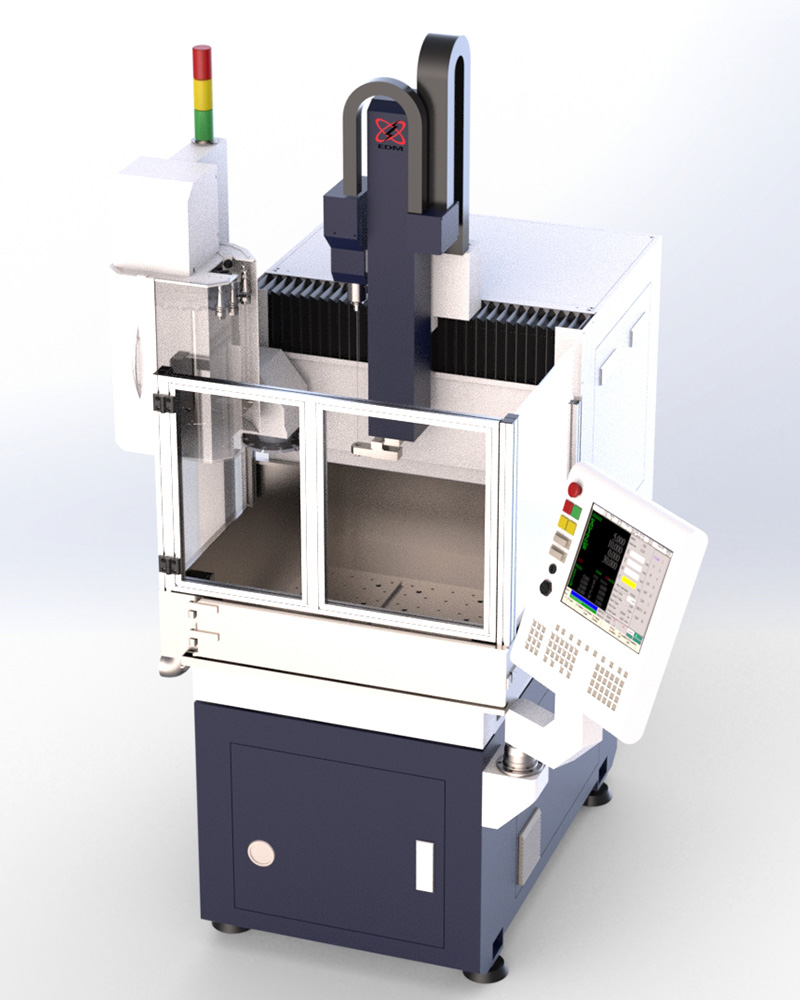
Belmont SY-3040TG with Light Curtains at IMTS 2024
Programmable flush pressure